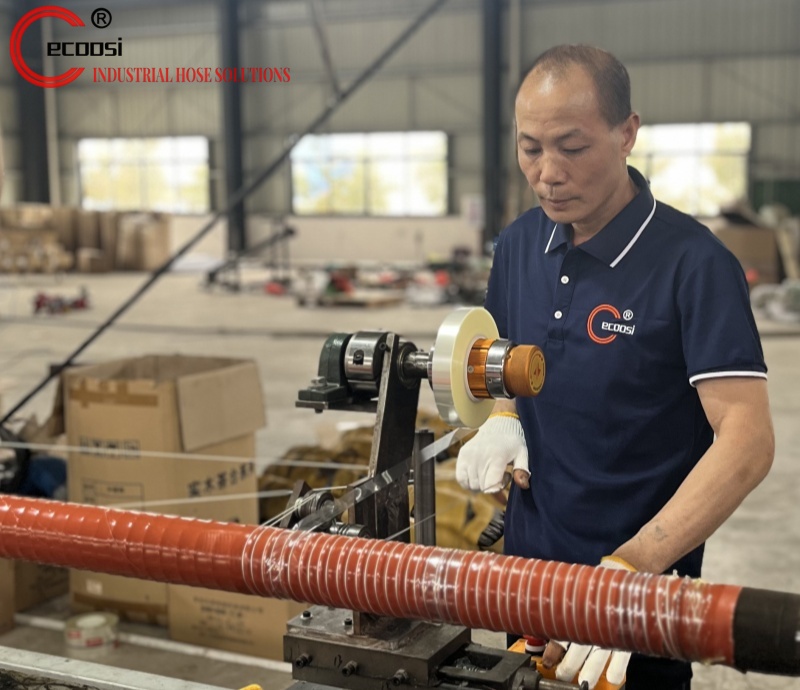
The Manufacturing Process of Silicone Duct Hose
Silicone duct hose is a versatile and durable component used across a wide range of industries, including automotive, aerospace, industrial, and medical applications. Known for its exceptional high temperature resistance, flexibility, and durability, it serves as a reliable solution for conveying air, fluids, and other materials in challenging environments. But how is this remarkable product made? In this article, we’ll explore the manufacturing process of silicone duct hose, breaking it down into its key stages.
What is Silicone Duct Hose?
Silicone duct hose is a flexible tube crafted from silicone rubber, a synthetic elastomer celebrated for its resistance to extreme temperatures, chemicals, and wear. Unlike traditional rubber or plastic hoses, silicone duct hose excels in harsh conditions, making it a go-to choice for applications like high-temperature exhaust systems, turbocharger connections, and industrial ventilation setups.
The Manufacturing Process
The production of silicone duct hose involves a series of precise steps: raw material preparation, extrusion, curing, reinforcement, and finishing. Let’s dive into each stage.
1. Raw Material Preparation
The journey begins with preparing the silicone rubber. This involves blending silicone polymers with fillers, pigments, and additives to achieve a putty-like consistency. The exact recipe can be tailored to meet specific needs—whether it’s enhanced temperature resistance, flexibility, or a particular color—ensuring the final product aligns with its intended use.
2. Extrusion
Next, the prepared silicone rubber is fed into an extruder, a machine that shapes the material by forcing it through a die. For duct hose, the die is engineered to form a hollow tube with precise inner and outer diameters. Two types of extruders are commonly used: single-screw, which is simpler and cost-effective but less consistent, and twin-screw, which offers superior mixing and output quality. The process demands careful control of temperature, pressure, and speed to maintain uniformity and quality in the extruded tube.
3. Curing
Freshly extruded, the silicone rubber tube remains soft and pliable. To transform it into a robust, durable material, it undergoes curing—typically by heating in an oven. This heat triggers cross-linking of the silicone molecules, hardening the structure. Depending on the hose’s size and thickness, curing can take several hours, locking in the properties that make silicone duct hose so resilient.
4. Reinforcement
For added strength and durability, many silicone duct hoses are reinforced. This step involves wrapping the extruded tube with materials like polyester fabric for burst resistance or embedding a wire helix to prevent collapse under vacuum. Reinforcement can occur before or after curing, depending on the design and application requirements.
5. Finishing
Once cured and reinforced, the hose is cut to its specified length. Additional finishing touches, such as attaching metal cuffs, clamps, or custom features like bends and branches, are added to meet the needs of its final application. This step ensures the hose is ready for installation and performance.
Variations in the Manufacturing Process
While the steps above outline the standard process, variations exist to suit specific hose types. For instance, mandrel wrapping—where silicone rubber is layered around a cylindrical form—is used for complex shapes or larger diameters. Curing methods can also differ, with alternatives like steam curing or room-temperature vulcanization (RTV) employed for certain products, offering flexibility in production.
Benefits of Silicone Duct Hose
The manufacturing process is designed to unlock silicone duct hose’s standout qualities:
High Temperature Resistance: It thrives in temperatures from -100°F to 500°F (-73°C to 260°C), perfect for extreme environments.
Flexibility: Its ability to bend without kinking or collapsing simplifies installation and use.
Durability: The cross-linked silicone structure resists wear, tear, and chemical damage.
Versatility: Customizable in size, shape, color, and reinforcement, it adapts to diverse needs.
A Brief History of Silicone Rubber
Silicone rubber’s story began in the 1940s, pioneered by researchers at Dow Corning and General Electric to meet the demands of aerospace and military applications. Its ability to endure extreme conditions made it indispensable, and over decades, it expanded into countless uses—medical devices, cookware, and, of course, duct hoses. Today, it remains a cornerstone of modern industry, evolving with advancements in technology and materials.
Conclusion
The manufacturing process of silicone duct hose is a blend of precision and innovation, from mixing raw materials to shaping, curing, and finishing the final product. Each step is crucial to delivering a hose that excels in demanding applications—whether in a car’s engine bay, an aircraft’s systems, or an industrial facility. Silicone duct hose stands as a testament to the power of advanced materials and meticulous craftsmanship, supporting industries worldwide with its unmatched performance.
Ecoosi specializes in manufacturing all kinds of silicone duct hoses. If you have questions or need additional information about our flexible duct hoses, please do not hesitate to click contact us or send an email to:info@eiduct.com or Whatsapp to:+86-187-1155-3123, or our other website:ductinghose.com, we will try our best to support you!