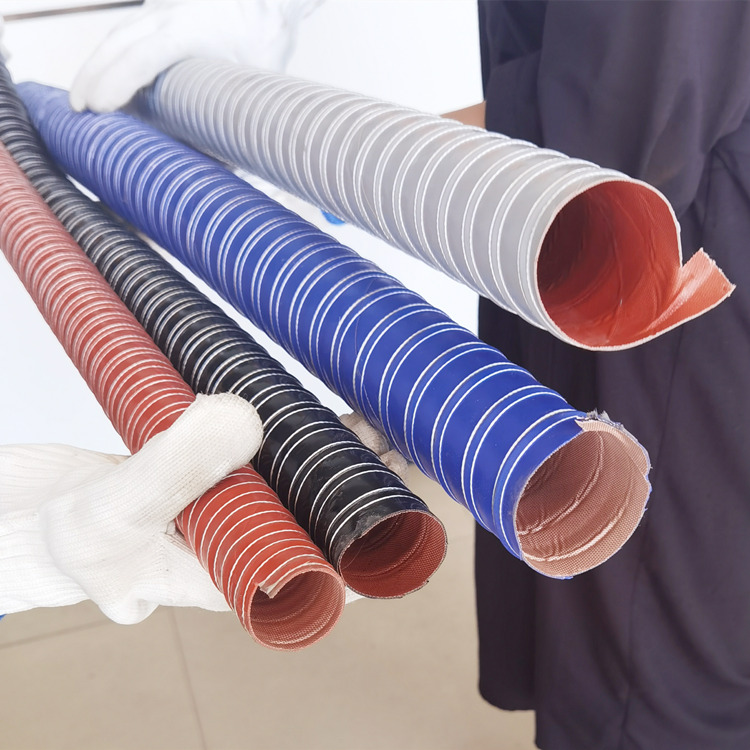
What is Silicone Ducting?
Silicone ducting is a specialized type of duct hose made from silicone rubber, designed for high-performance applications that involve extreme temperatures, chemical exposure, or challenging environmental conditions. Due to its flexibility, heat resistance, and durability, silicone ducting is widely used in industries such as aerospace, automotive, industrial ventilation, and more. In this article, we’ll explore what silicone ducting is, how it’s made, its key features, and the various applications where it is most effective.
1. Silicone Ducting Explained
Silicone ducting is a flexible hose designed to transport air, gases, fumes, or materials through a duct system in environments where ordinary ducting materials wouldn’t hold up. What sets silicone ducting apart is its ability to withstand extreme heat and cold, resist chemical degradation, and maintain flexibility even in challenging environments.
Unlike other ducting materials like PVC or polyurethane, silicone is highly resistant to cracking, drying out, or becoming brittle when exposed to high temperatures or UV light, making it a preferred option for both industrial and specialized applications.
2. How is Silicone Ducting Made?
Silicone ducting is manufactured from silicone rubber, a synthetic material that remains stable across a wide temperature range. Here’s a quick overview of the manufacturing process:
Base Material: Silicone rubber is produced by curing liquid silicone into solid, flexible rubber. This material is known for its excellent temperature tolerance and flexibility.
Reinforcement: Many silicone duct hoses are reinforced with a wire helix, fabric, or fiberglass lining. This reinforcement provides additional strength and shape retention, allowing the hose to handle high-pressure airflows and preventing collapse during use.
Vulcanization: To enhance its durability and thermal stability, the silicone rubber undergoes a vulcanization process, which helps create a long-lasting product capable of withstanding harsh conditions.
For production video please click video of silicone ducting.
3. Key Features of Silicone Ducting
Silicone ducting is a popular choice for many industries due to its combination of unique features. Here are the key advantages that make silicone ducting a go-to solution for specialized ducting needs:
1. High-Temperature Resistance
Silicone ducting can withstand extreme heat, often up to 550°F (290°C), with some high-performance varieties rated for even higher temperatures. This makes it ideal for applications involving exhaust systems, engine ventilation, or industrial processes where heat management is crucial.
2. Cold Resistance
Silicone maintains flexibility in cold temperatures, as low as -100°F (-73°C), without becoming brittle or losing its structural integrity. This makes it suitable for use in cold storage or refrigeration applications.
3. Chemical Resistance
Silicone is resistant to a wide range of chemicals, including oils, solvents, and other corrosive substances. This property ensures longevity even in environments where other materials might degrade due to chemical exposure.
4. Flexibility
Despite its durability, silicone remains highly flexible, allowing it to bend around tight corners or in confined spaces without kinking or breaking. This is essential in applications where space constraints require ducting to adapt to complex setups.
5. Durability and Longevity
Silicone ducting is UV-resistant, meaning it won’t degrade when exposed to sunlight or outdoor elements. It also resists cracking, tearing, and general wear and tear, ensuring a long service life.
6. Non-Toxic and Safe
Silicone is non-toxic and safe to use in food processing, medical, or other applications that require clean, non-reactive materials. It doesn’t emit harmful fumes, making it suitable for safe air movement.
4. Applications of Silicone Ducting
Due to its unique properties, silicone ducting is used in a variety of industries where conventional duct hoses would fail. Here are some common applications:
1. Aerospace and Automotive
In aircraft and automobiles, silicone ducting is used in ventilation systems, engine exhaust systems, and turbocharging setups due to its heat resistance and flexibility. It can handle the intense heat generated by engines while maintaining structural integrity and performance.
2. Industrial Ventilation
Many industrial processes, such as welding, foundry operations, or chemical processing, produce hot fumes or gases that need to be safely vented. Silicone ducting is ideal for these environments, providing safe and reliable fume extraction and air handling.
3. HVAC Systems
In heating, ventilation, and air conditioning systems, silicone ducting is used where temperature extremes exist, such as in high-temperature air flows or outdoor HVAC units exposed to varying weather conditions.
4. Food Processing
The food industry often requires ducting that is not only durable but also non-toxic and resistant to high temperatures. Silicone ducting is used in food processing equipment, especially for transferring air or hot vapors in a clean, sanitary manner.
5. Exhaust Systems
Silicone ducting is frequently used in industrial exhaust systems to transport hot fumes, engine exhaust, and other gases safely. Its heat tolerance ensures it won’t degrade under high exhaust temperatures, making it a reliable option for continuous operation.
6. Laboratories and Chemical Plants
For environments that deal with hazardous fumes or chemical reactions, silicone ducting’s resistance to corrosive materials makes it the ideal choice. It ensures safe extraction and transportation of harmful gases or particles, protecting both workers and equipment.
7. Medical and Pharmaceutical Applications
Silicone ducting is often chosen for clean environments, such as hospitals or pharmaceutical labs, because it’s non-reactive, non-toxic, and can be sterilized easily. It is used in cleanrooms or in transferring air in medical equipment.
5. Choosing the Right Silicone Ducting for Your Needs
When selecting silicone ducting for your specific application, it’s important to consider factors such as:
Temperature Range: Make sure the silicone ducting you choose can handle the maximum temperatures of your application.
Flexibility: If your ducting needs to navigate tight spaces or sharp corners, opt for a more flexible, reinforced option.
Chemical Exposure: Ensure that the duct hose is rated for any chemicals or substances it will encounter.
Pressure Rating: Some applications may require ducting that can handle high air pressure or vacuum conditions. In these cases, a reinforced silicone duct hose with a spiral wire helix may be necessary.
Conclusion
Silicone ducting is a highly versatile and durable solution for applications that involve extreme temperatures, chemical exposure, and the need for flexibility. Its ability to perform reliably under harsh conditions makes it a popular choice across multiple industries, from automotive to industrial ventilation and beyond.
By understanding the key properties of silicone ducting, you can make informed decisions when selecting the right hose for your specific needs, ensuring long-lasting performance and improved efficiency in your operations. Whether you’re looking to manage exhaust fumes, ventilate high-temperature environments, or handle chemical-laden air, silicone ducting offers the reliability and safety needed for demanding applications.
You could also please feel free to click contact us or send an email to:info@eiduct.com or Whatsapp to:+86-187-1155-3123,or our other website:ductinghose.com, we will try our best to support you!